Which are the main benefits of gear grinding?
At Tasowheel, one of the hallmarks of our production is gear grinding. The method we put emphasis on is generating grinding mainly due to its efficiency and faster production rates compared to other methods. Generating grinding is based on grinding worm and gear wheel operating similar to a worm – wormwheel pair. In other words, grinding worm with a profile matching the manufactured gear, will be fed tangentially towards the gear forming a evolvent profile.
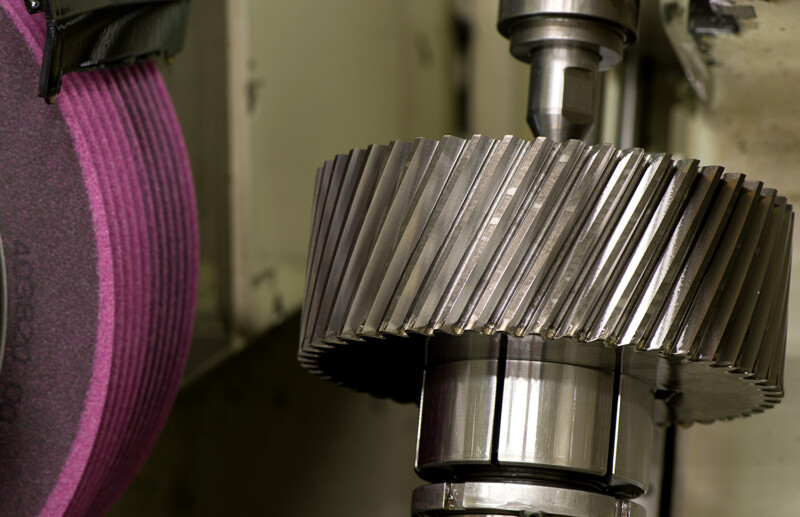
Our technical specialist Lauri Mäkelä lists the main benefits of gear grinding:
- Precision and accuracy: Gear grinding is used to achieve high levels of precision and accuracy in the gear’s tooth profile, size, and pitch. This ensures that the gears operate smoothly, minimizing any variations in motion and reducing wear and tear.
- Noise reduction: The grinding process eliminates irregularities in the tooth surfaces, which reduces gear noise and vibration during operation.
- Increased load-carrying capacity: Gear grinding enhances the tooth’s load-carrying capacity by helping to distribute the load evenly across the teeth.
- Efficiency and performance: Ground gears have lower friction losses during operation, which improves overall efficiency and performance of the gear system.
- Tailored gear profiles: Grinding enables the production of customized gear profiles for specific applications. This can be done by profiling the grinding worm with the desired gear profile and grinding the required flank modifications.
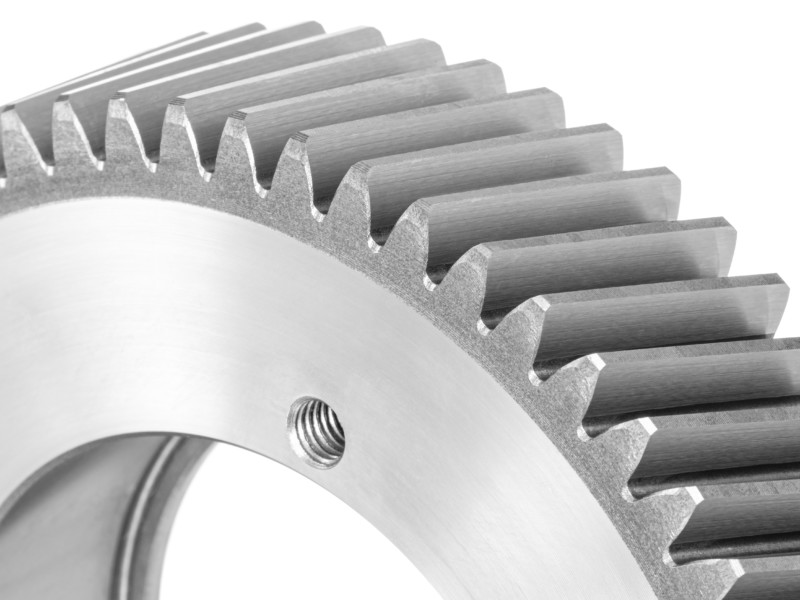
Gear grinding requires advanced machines, skilled operators and rigorous quality control, which are the cornerstones of the Tasowheel production. Additionally, we foster a culture of continuous improvement, which is vital for adopting new technologies and refining processes to enhance precision and efficiency in gear grinding.